Flexible Coupling Applications Overview
Couplings are a common component found in various shaft-driven machinery. They connect two separate pole-like components known as shafts. Motors provide mechanical power called Torque to shaft-driven machinery. However, if the shafts between these endpoints are not aligning and redesigning costs are too much, then flexible couplings are an affordable alternative. Generally speaking, there two types of flexible couplings: mechanically flexible couplings that rely on its design to provide clearance between components for movement, and flexible element couplings that rely on elastic components to overcome shaft misalignment and operational backlash. Flexible couplings are subject to wear and abrasion due to operation workloads, shaft speeds and torque capacity, but there are various coupling types and materials that can save both time and maintenance costs that fit operational and/or environmental needs.
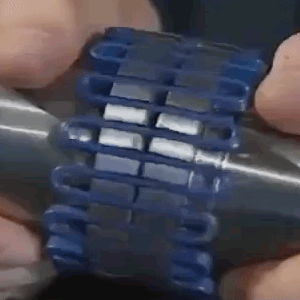
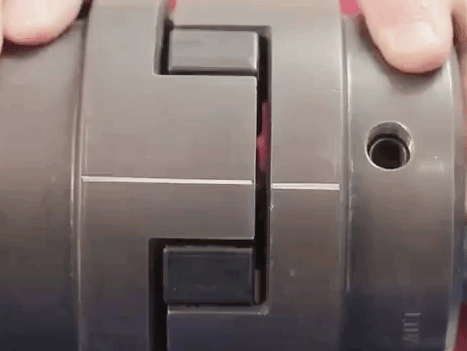
(L). mechanically flexible: Grid coupling is designed with a metal coil that allows enough slack for movement. (R). flexible element: Jaw couplings rely on elastic elements that will compress during operations.
While there are some coupling variations that are designed to specifically accommodate misalignment, proper installation remains crucial to reduce future maintenance costs. Routine cleaning and inspections of visual indicators (wear and tear), new sounds, temperature, chemical resistance all play a role in diagnosing faulty coupling behavior. A failing coupling may not be properly installed, or it isn’t well-suited for its environment or the operations asked of it. Here, I will provide a brief overview of the main types of couplings and where they are best applied.

*Elastomeric inserts maintain effective power transmission even if angular misalignment occurs.
Jaw Coupling Applications
Jaw Couplings are flexible element couplings that have two jaw-like hubs and an interlocking rubber-like insert known as the Spider. The Spider protects the hub components and assists with potential misalignments due to the elastic nature of the Spider. Elasticity means Spiders can be compressed, reducing and dampening shock and vibrations produced from operations. Small amounts of backlash are desirable for protecting components, but significant backlash will wear down components and hinder actions that require more accurate motion. However, accurate motion technologies like servomotors can implement Curved Spider designs to perform with zero-backlash.
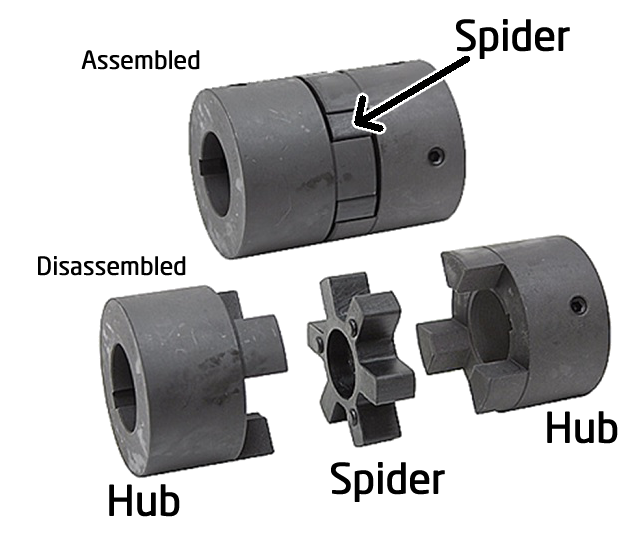
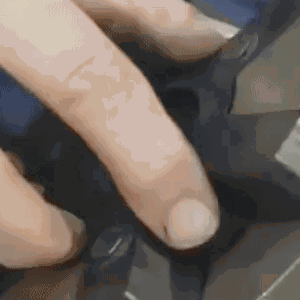
If the spider fails, the hub teeth will interlock and continue to transfer torque between the two shafts. Hubs will wear down if Spiders are not replaced accordingly. Alternatively, In-shear variations are designed to prevent this fail-safe behavior. In-shear designs space the hubs apart, removing the ability to remain interlocked after the insert fails - halting operations from further component damage. The applications for these respective behaviors depends entirely on maintenance and the operations needs. Jaw couplings offer a wide selection of designs, inserts materials and therefore suit the needs any shaft-driven system.
*Clearance between hub teeth and spiders accommodates possible shaft misalignment with added backlash, or spiders can be fitted to completely reduce backlash entirely.
Grid Coupling Applications
Generally, Grid couplings are considered on par with gear and insert-based (JAW) couplings. Grid coupling owes its flexibility and shock resistance to its unique spring-like design, which uses a flexible metal grid that provides clearance, protection and reduced shock impact for the hub teeth. There is even a degree of vibration dampening capability, which is uncharacteristic for most metal only couplings. However, like most flexible metal couplings, routine use of lubrication is a must for peak performance for your grid couplings.
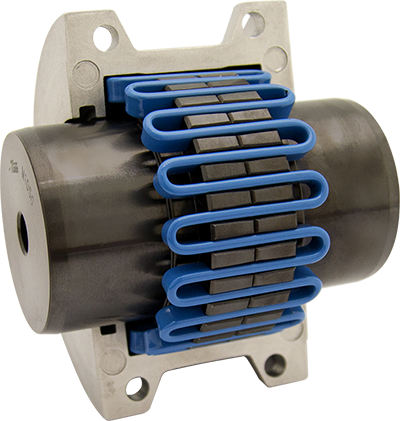
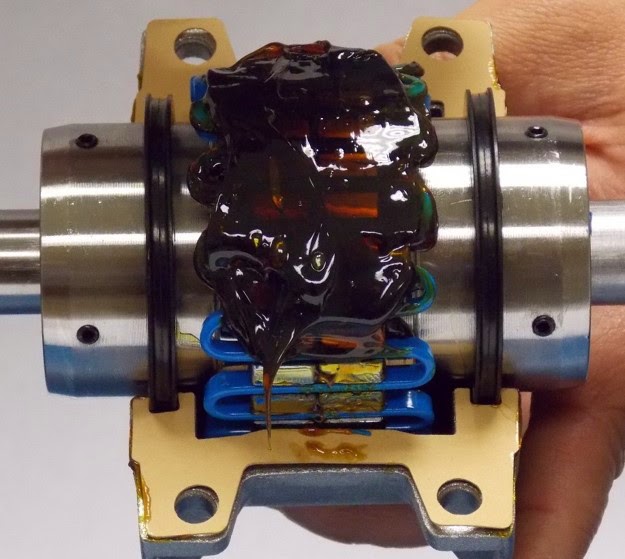
Like Jaw and Gear Couplings, Grid Couplings are highly versatile and its metal components make it more durable than Jaw couplings, and its grid is just as interchangeable to better suit operational needs.
*Even a good coupling will still fail if not properly maintained! Without lubrication, the metal on metal contact will cause wear on hub teeth and the grid itself.
Gear Coupling Application
Gear couplings are plainly characterized by the meshing of the internal teeth found on the sleeve and external teeth on the hub. The teeth can be crowned to afford more clearance when intermeshed, which greatly improves the ability to accommodate any angular misalignment issues.

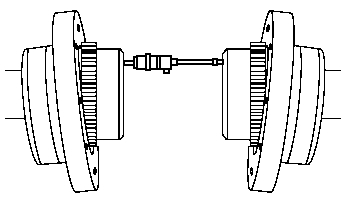
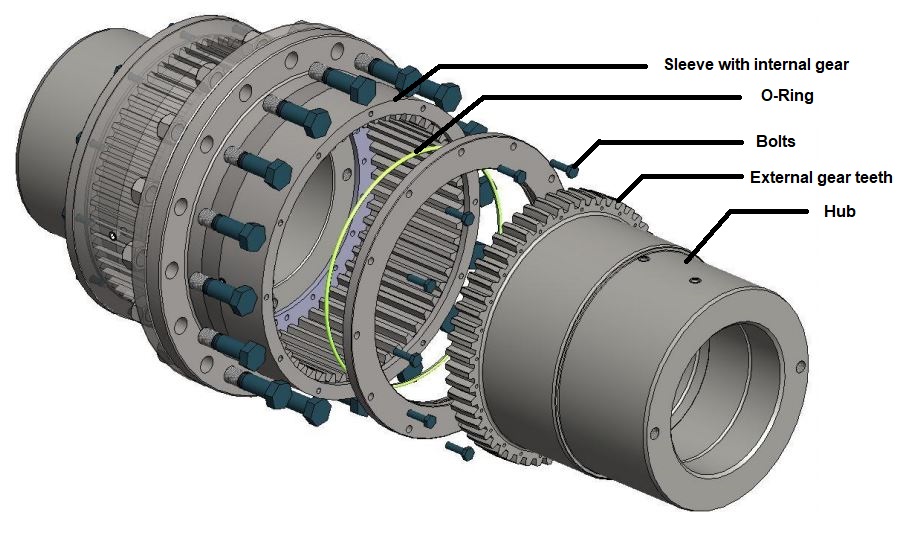
Gear couplings are good for torque-intensive technologies such as cranes, conveyors and various other big operations. Gear Couplings provide one of the highest torque amounts Gear Couplings drive purely with metal on metal transmission. This also means that abrupt operations that cause shock will wear down components and will require routine lubrication. Poorly maintained Gear Couplings often requires a complete replacement for possibly greater costs.
Disc Coupling Applications
Disc couplings are another common flexible element type coupling suited for high speed, high torque operations found in motion control. The flexible component are called disc packs, flat metal rings that flex and distribute its tension evenly, which is a suitable solution for angular shaft misalignments issues. The disc pack also uses bolts to help retain a measure of rigidty as it secures all the components together. Flexibility can also be increased with the coupling's amount of disc packs, or when using thinner ring components. Additionally, decreasing the amount of bolt holes in a disc pack provides more flexible surface area and reduced coupling rigidity.
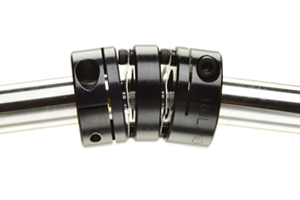
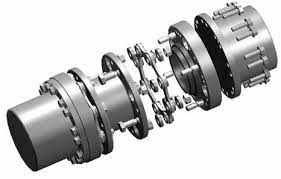
*Disc coupling features numerous components, so refer to best practices to avoid improper use.
Diaphragm Coupling Applications
Diaphragm couplings are capable of high-speed, high-torque operations, which can be attributed to its one or many metallic membranes called diaphragms. These diaphragms are notably large and flexible towards its center, allowing it to warp to accommodate any shaft misalignment, not just angular misalignment. However the differences of diaphragm’s diameter, thickness and shape between the inner and outer diameters determine the torque capacity and flexibility.
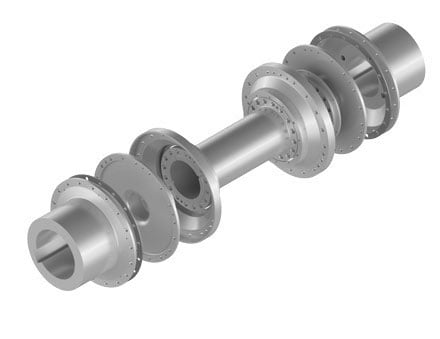
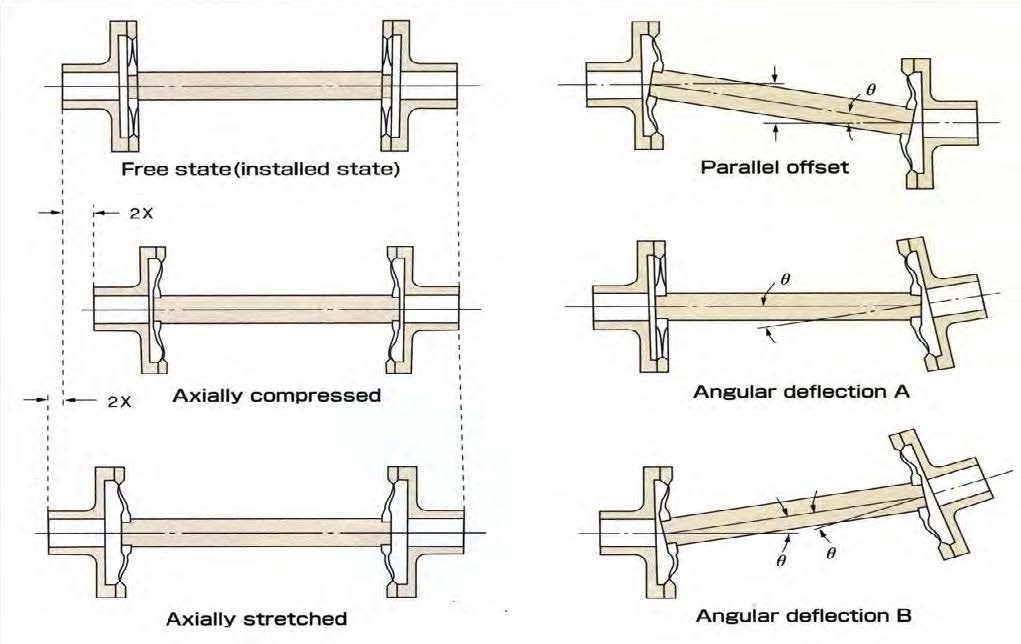
Diaphragm shares similarities and applications with disc couplings, often found in compression technologies and motors. Diaphragm couplings are larger, but gain greater torque ability over the disc couplings. In case if either flexible elements fail, Diaphragm couplings will no longer transmit torque, separating upon failure, and disc couplings will continue to function only if its bolts can withstand the load from operations.
Beam Coupling Applications
The coil-like beam couplings are mechanically flexible couplings that can easily accommodate any angular misalignment between driving and driven shafts. These types of couplings consist of only one component, as the entire device was created from subtracting the material into a coil-like beam. This allows the coupling to remain durable and negate operational backlash entirely. While increasing the amount of coils increases the flexibility, and increasing the number of beams improves rigidity, these kinds of couplings are not well suited for moderate or heavier loads.
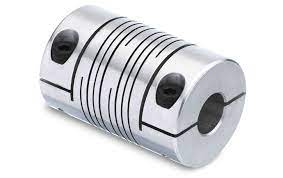
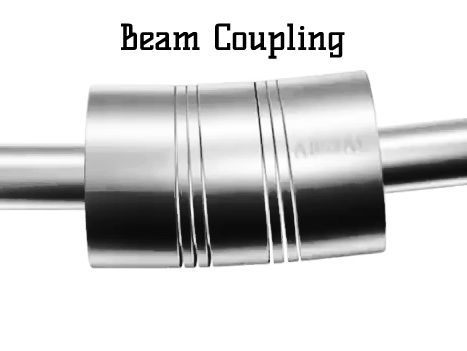
*The beam coupling contorts while the being driven at high speeds, making it a suitable for transmitting torque when coupling flexibility is desired.
The beam couplings one material design also comes with the limitations of what can be used to make them, thus, limiting the range of its applications in addition to its workload constrictions. These couplings are favored in robotics and motion control that would greatly benefit from its flexible applications.
Chain Coupling Applications
Chain couplings are an old staple for mechanically flexible couplings, and a cheaper alternative for basic coupling uses. These couplings use a distinctive chain with rollers that hook around the hub teeth, securing the hubs together with minimal clearance for angular misalignment. These chains can be made either from metal or plastic which have their own benefits and disadvantages. Metal chains need covers and lubrication, but can transmit more torque than its plastic counterparts. Both produce noise, but there are silent variants that can reduce those effects.
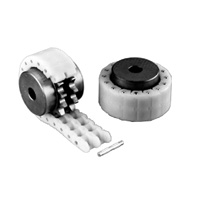
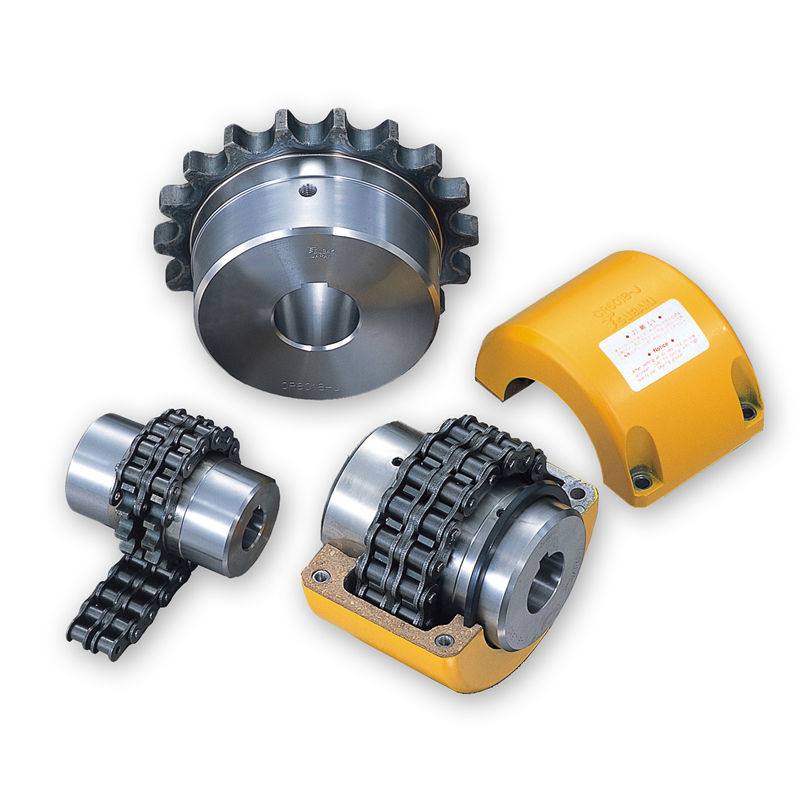
The uses of chain couplings are limited to operations on low-moderate speeds with high torque requirements like conveyor or line-shaft technologies. They do not handle shock impact well as there are other impact-resistant couplings better suited for stop and go operations (Jaw, Grid, etc.). However, since chain couplings are cheaper and easier to install, its use is still prevalent today.
Oldham Coupling Applications
The Oldham coupling design incorporates a sliding disc element the slots between two hubs with teeth perpendicular to each other. This allows the Oldham coupling to significantly accommodate parallel misalignment, and is able to modestly accommodate angular and axial shaft misalignment. The disk is crucial for transmitting torque, but this coupling type cannot withstand high operation loads. If the load is too high the disk in the center will break. There is a benefit here however - if the disk breaks everything else tends to stay undamaged and those disks are cheap and easy to replace. If there are some high value components at the other ends (expensive motors, etc), they can be saved with this type of coupling, whereas with others the risk of component damage is far greater. Additionally, the material types available for these disks is quite varied, giving the user a lot of options
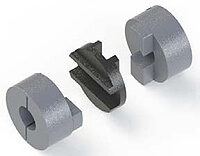
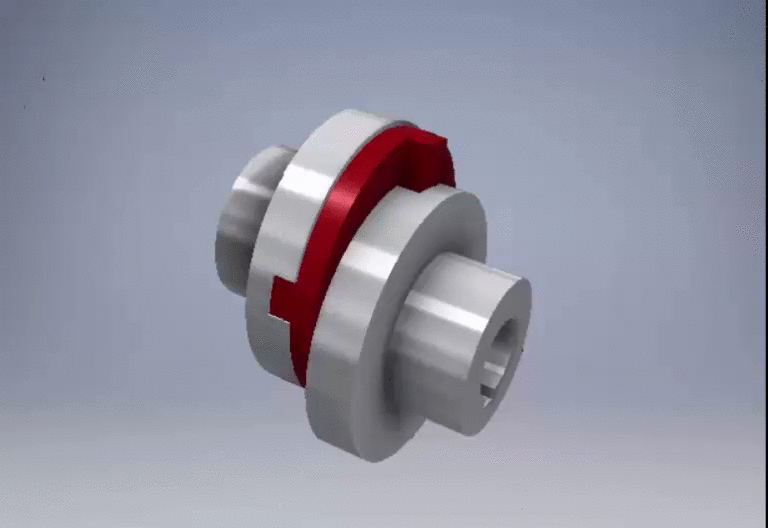
Torsional Coupling Applications
Torsional Couplings are designed to combat and reduce the effects of torsional vibrations produced from torque transmission. When this twisting-type of vibration occurs it can cause devastating damage to the equipment. Torsional couplings can be installed to keep transmission systems from reaching their natural frequency. However, it is highly advised to have an expert conduct a torsional vibration analysis before assembling the rotation system, and redesign and implement the necessary components (couplings) to prevent torsional vibrations. These couplings tune shaft speeds and can be mounted directly to flywheels or power take-off (PTO) components. *Flywheels store shaft driven power, and PTOs “take away” power from systems.
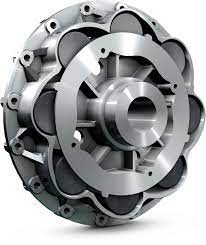
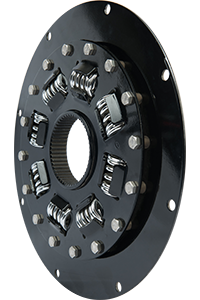
(L). Elastomer insert type Torsional Coupling. (R). Steel spring type Torsional coupling. Torsional Coupling, also known as a clutch plate as they often found in commercial vehicles or racing cars.
There are generally two variations that exist, both utilize specific elements to dampen any natural frequencies that occur at specific speeds. As we already know by now, elastomer insert types are inherently flexible, and requires less complex engineering feats to assemble. However if a certain stiffness is required, the spring type is well suited for extreme load capacities. As long the spring types are kept lubricated, they will remain durable and could withstand extreme temperatures that an elastomer type cannot.
Final Note
The world of couplings is boundless with many variations, configurations, and applications, thus selecting the right coupling depends entirely on operational needs and maintenance. Proper installation and understanding the limitations of the chosen couplings will make all the difference in avoiding critical failure. No operation is without couplings, so always refer to the specifications of couplings if there is any uncertainty.
Image Sources
- Selecting a Coupling for a Shaft RedVectorOnline, https://www.youtube.com/watch?v=A2UbzFyPA6k
- Shaft Alignment Concepts: Controlling Backlash | ACOEM Acoem USA, https://www.youtube.com/watch?v=AnNfrW7EqCk
- Shaft Alignment Basics: Couplings Explained | ACOEM Acoem USA, https://www.youtube.com/watch?v=HBNJmGF5SO0
- Lovejoy Style Couplings A&E Bearing & Hydraulics, https://www.aebearing.com/lovejoy-styled-couplers
- Martin Grid Couplings' Blue-Flex Design is Built to Withstand Extreme Torque IBT Inc, https://www.ibtinc.com/martin-grid-couplings-built-for-torque/
- How should you pack the grease in a Grid Coupling? Elliot Wilson, http://www.couplinganswers.com/2014/12/how-should-you-pack-grease-in-grid.html
- Amerigear Gear Couplings Metal Labyrinth Seal Ameridrives, https://www.ameridrives.com/products/amerigear-couplings
- Gear Coupling Styles and Options Drive Components, https://www.drivecomponentsllc.com/gear-couplings/
- The Basic function of a Gear Coupling Team Stuffworking, https://www.stuffworking.com/basic-function-of-a-gear-coupling/
- What to Look for In a Servo Coupling Ruland, https://www.ruland.com/technical-resources/technical-articles/technical-article-servo-coupling
- Disc Couplings - Common Terminology (Part 2) Elliot Wilson, http://www.couplinganswers.com/2015/09/
- Torque Density vs. Durability Charlie Kopplin, https://modernpumpingtoday.com/torque-density-vs-durability/
- Kop-Flex Coupling Selection and Design Regal, https://www.regalbeloit.com/brands/Kop-Flex/Coupling-Selection-And-Design
- EKK/Eagle Diaphragm Coupling RevolCouplings http://www.revolutionptc.com/cdiap.html#/
- Multi-Beam Couplings | Huco Dynatork Altra Motion, https://www.altramotion.com/market/motion-control/automated-assembly/couplings/multi-beam-couplings
- Shaft couplings from Abssac ABSSACLTD, https://www.youtube.com/watch?v=NfdTES0ZWNU
- Engineering Plastic Coupling Use Chain Only Misumi, https://uk.misumi-ec.com/vona2/detail/221000014662/#
- Tsubakimoto Chain Tsubaki, https://www.directindustry.com/prod/tsubakimoto-chain/product-5083-39945.html
- SureMotion Oldham Drive Couplings AutomationDirect, https://www.automationdirect.com/adc/overview/catalog/power_transmission_(mechanical)/drive_couplings/oldham_couplings
- Oldham Coupling Animated Anas Abdullah, https://grabcad.com/library/oldham-coupling-animated-1
- Flexible Coupling CENTAFLEX-R Direct Industry, https://www.directindustry.com/prod/centa-power-transmission/product-9279-718095.html
- About Us Torsion Control Products, https://www.torsioncontrol.com/