- Home
- Popular products
- Advantages and Disadvantages of Helical Gears
Advantages and Disadvantages of Helical Gears
Helical gears are a type of cylindrical gear. They feature teeth that are curved in the shape of a helix - cut at an angle to the axis of the gear. Because of this, the line of contact between each tooth is inclined. The contact between two teeth is gradual; it starts at one end of the tooth and progresses to line contact as the gear rotates. Unlike spur gears, at no time is the full length of a tooth completely engaged.
Helical gears are commonly used in automotive transmissions. They are often chosen for high-speed applications such as hotel and catering industry machinery. These gears are also ideal for high load applications. They are often chosen over spur gears for applications that have non-parallel shafts.
Other industries where helical gears are commonly used include steel and rolling mills, printing, textile industries, plastic industries, and food industries. You can find helical gears in conveyors, elevators, blowers, compressors, and cutters.
Advantages of Helical Gears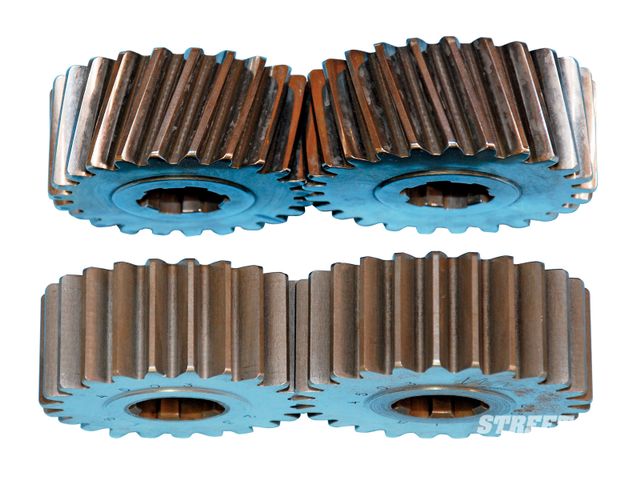
- Helical gears can be used with both parallel and non-parallel shafts.
- Because the teeth engage more gradually, helical gears offer smoother gear operation, reducing shock loads and causing less noise and vibration. This makes them ideal for high-speed applications where noise abatement is a requirement.
- Helical gears are more durable. They have a higher number of teeth which means less load is placed on each tooth which results in less wear.
- Helical gears have a high load-carrying capacity. Its teeth, which are diagonally positioned, are larger in number and length, increasing the surface area of contact. In addition, the teeth are always in mesh which enables the gears to distribute the load among several axes at all times.
Disadvantages of Helical Gears
- Helical gears typically have a higher manufacturing cost compared to spur gears.
- Helical gears generate a large amount of thrust force due to the helix angle which requires the use of thrust bearings to absorb and support this force.
- Higher friction due to the sliding action requires the use of lubricants.
- This sliding contact also generates heat which results in power loss and reduced efficiency.
Should I use helical gears?
Spur gears have a simple design making them easy to manufacture and install. They're also more efficient compared to helical gears of the same size. However, helical gears have several significant advantages to spur gears. They can be used in the same type of applications such as generators and pumps, but they offer a smoother and quieter operation. The increased torque carrying capacity of helical gears also make them a better option. In addition, these gears are more durable and can be used with parallel and non-parallel shafts.
Simply put, you should choose spur gears if you require a simple design, more efficient power transmission, and low to medium speed where noise is not a factor. Other than that, helical gears are the better choice.