- Home
- Popular products
- Hydrostatic vs Hydrodynamic bearings
Hydrostatic vs Hydrodynamic Bearings
If you have heavy industrial equipment that is powered by shaft driven technology, then it is very likely that you are already using fluid film bearings. If that isn't the case, then you should consider relying on fluid bearings instead of their rolling element counterparts - the reasons why will be discussed in detail later in this article. Before we try to understand the advantages between these bearing types, I believe it is important to illustrate the function and importance that bearings have in industrial settings. We'll first take a look at what bearings are, and what they can accomplish. Then we will dive further into the fluid bearing types: Hydrostatic and Hydrodynamic bearings and how they can possibly last forever.
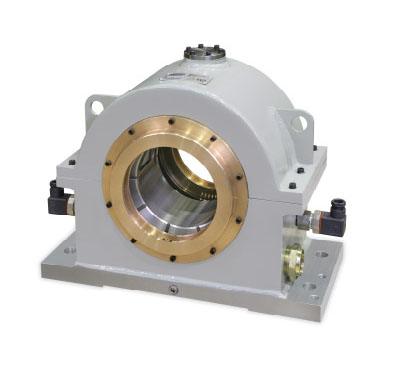
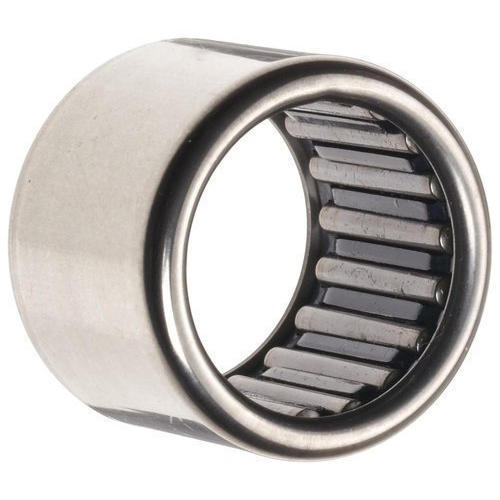
Left is an example of a fluid film bearing inside a split style housing. Right is an example of a rolling element bearing, needle rollers.
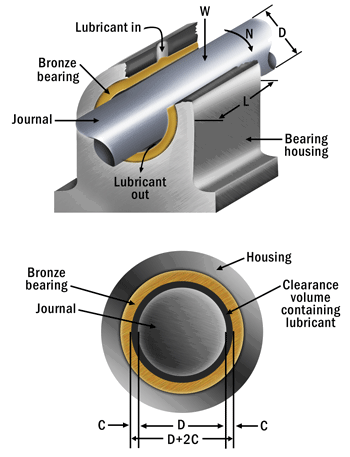
What are Bearings?
Bearings are key mechanical components designed to encourage the movement of other connected components. In most cases, this is the shaft, a pole-like structure that extends rotary forces to other mechanisms. Typically, shafts are directly or indirectly driven by motors, but bearings can further rotary, or linear motion by reducing the friction between the bearing's inner elements - there are many types of bearings, each with unique methods and inner elements. We'll be focusing primarily on rotary bearings that are limited to rotary motion, but there are linear bearings that can perform linear movement.
You will see lots of rotary bearings in shaft systems and shafts can be rotating elements themselves. Notably, shafts made with comparatively tough metal like carbon steel or stainless steel. Certain bearing surfaces can made with softer metals like Babbitt, to help reduce friction, and damage from metal on metal contact. However the shaft's health can be preserved more by reinforcing the area where the bearing and shaft is connected - this is called the journal. The journal is reinforced with durable chromium alloys, making it much easier for the bearing to wear down first to help preserve the more expensive shaft. However this is not always the case with all bearings. There are bearings that do not wear as long as proper measures have been taken to maintain these bearings. Enter fluid bearings.
Fluid Bearings: Hydrostatic
Fluid bearings reduce friction through the use of fluids, specifically lubricants. Due to the spatial clearance between the shaft and the housing space within the bearing, the neutral position of a shaft is always asymmetrical, but never centered within the bearing - the shaft is consequently touching the bearing surface. The goal of fluid bearings is to use its lubricants to lift and suspend the shaft so there is no metal on metal contact between the shaft's journal and the bearing surface. The lubricant must undergo enough pressure to form a layer that converge between the journal and the bearing, which should be enough to lift the shaft. Hydrostatic variants of fluid bearings rely on external pumps to maintain constant pressure within the bearing. Pumps introduce more complexity and observation to a fluid bearings maintenance routine, but it could also eliminate any future costs as a result.
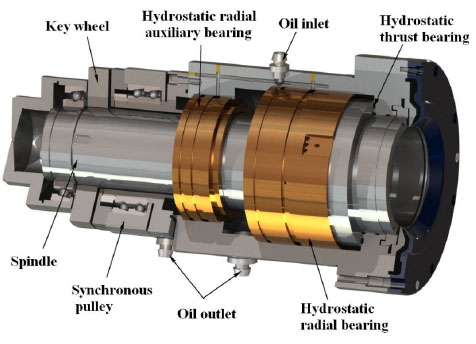
Multiple hydrostatic bearings can be used in tandem to support large shafts. Note the oil inlets/outlets for lubricant pressure control via pump.
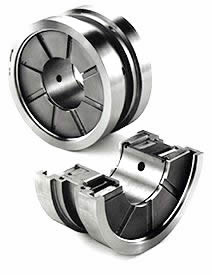
Fluid Bearings: Hydrodynamic
In contrast to hydrostatic fluid bearings, hydrodynamic bearings use shaft rotation speeds to produce the fluid flim layer. The lubricant in hydrodynamic fluid bearings are not always entirely filled, instead there could be just enough lubricant to permit a process phenomenon otherwise referred to as pressure wedge. It is this pressure wedge that lifts the shaft from the bearing surface, preventing metal on metal contact during rotations. Multiple factors help create the pressure wedge: speed of the shaft's rotation, the viscosity or stickness of the lubricant, and the force exerted from the load onto the shaft. What makes these bearings more dynamic is because there is no need for any external pumps to constantly supply the necessary pressure. However, these bearings can suffer from significant wear at startup and shutdown phases where the lubricant is forced out as the shaft and the bearing surface returns to its neutral state. To avoid wear at these phases may require a secondary bearing or a pump to accommodate friction.
Advantages and Disadvantages over Roller bearings
Fluid bearings triumph when operations demand high loads, at high or low speeds. Fluid bearings are more reliable for heavy equipment than the brittle design of roller bearings. Roller bearings are complicated components with many intricate inner elements. They sport outer and inner rings called races that serves as a continuous track for the rolling elements. The rolling elements can be caged or not, but they all share a minimal surface area. With a lack surface area to bear the load, heavier loads will cause both roller and ball bearings to fail - meaning more maintenance and replacements for said bearings. Conversely, fluid bearings are quite capable of easily outlasting rolling element bearings, but that usually requires monitoring the bearing and always adjusting pressure, or rotation speeds. If operation conditions kept and oil leaks risk equipment damage, then consider using roller or even newer magnetic bearings over fluid bearings. Some fluid bearings can be challenging to set up, as there are many combined factors that generate the supporting oil layer. Hydrostatic bearings need external pump require calculations and constant pressure to support the shaft, and hydrodynamic bearings risk wear at key phases when it is no longer rotating.
Conclusion
Hopefully this article has helped clarify any questions about fluid bearings and help you find value in their versatility - non-fluid bearings that can sustain high loads at high and slow speeds most likely have to be machined specifically to accommodate such conditons. As long as you understand what it takes to take care of these bearings, they will last you for a lifetime.
Image Credits
- Fluid Film Bearings WAUKESHA Bearings, https://www.waukbearing.com/products/fluid-film-bearings/
- China Metal Needle Roller Bearing Indiamart, https://www.indiamart.com/proddetail/needle-roller-bearing-11740438748.html
- Determining Proper Oil Flow to Journal Bearings Noria Corporation, https://www.machinerylubrication.com/Read/29654/journal-bearing-oil
- Numerical Simulation and Experimental Study of the Hydrostatic Spindle with Orifice Restrictors The Open Mechanical Engineering Journal, http://volinsky.myweb.usf.edu/Spindle.pdf
- Hydrostatic and Hydrodynamic Bearings Information GlobalSpec, https://www.globalspec.com/learnmore/mechanical_components/bearings_bushings/hydrostatic_hydrodynamic_bearings